The Science Behind Porosity: A Comprehensive Guide for Welders and Fabricators
Comprehending the elaborate systems behind porosity in welding is vital for welders and fabricators aiming for flawless craftsmanship. As metalworkers delve into the depths of this sensation, they discover a world controlled by various factors that affect the formation of these tiny voids within welds. From the structure of the base materials to the ins and outs of the welding process itself, a wide variety of variables conspire to either worsen or reduce the visibility of porosity. In this thorough guide, we will certainly decipher the science behind porosity, discovering its effects on weld high quality and introduction advanced strategies for its control. Join us on this journey via the microcosm of welding blemishes, where accuracy meets understanding in the search of remarkable welds.
Recognizing Porosity in Welding
FIRST SENTENCE:
Evaluation of porosity in welding reveals crucial understandings right into the stability and quality of the weld joint. Porosity, defined by the presence of cavities or spaces within the weld steel, is an usual problem in welding procedures. These gaps, if not effectively resolved, can jeopardize the architectural honesty and mechanical buildings of the weld, bring about prospective failings in the completed item.
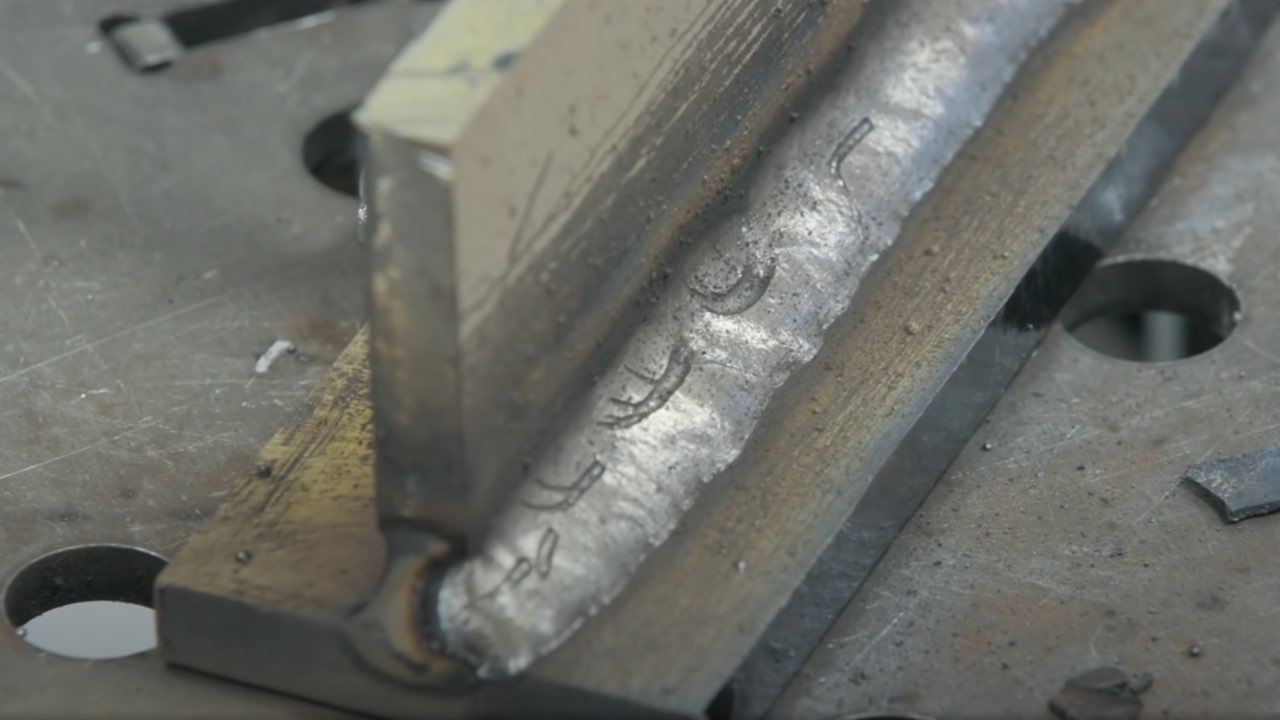
To spot and quantify porosity, non-destructive testing methods such as ultrasonic screening or X-ray evaluation are typically utilized. These methods permit for the recognition of interior flaws without endangering the honesty of the weld. By assessing the dimension, form, and circulation of porosity within a weld, welders can make educated decisions to improve their welding processes and attain sounder weld joints.
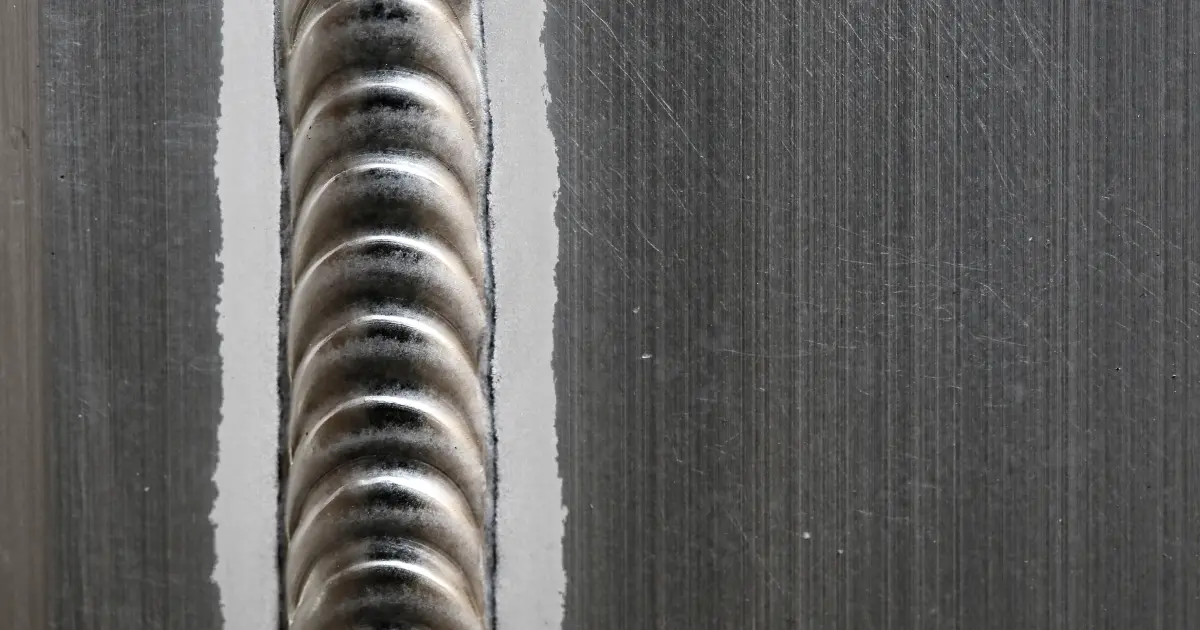
Elements Affecting Porosity Development
The incident of porosity in welding is influenced by a myriad of elements, varying from gas protecting effectiveness to the ins and outs of welding criterion settings. One important aspect adding to porosity development is inadequate gas securing. When the shielding gas, typically argon or carbon dioxide, is not successfully covering the weld swimming pool, climatic gases like oxygen and nitrogen can contaminate the liquified steel, causing porosity. Furthermore, the sanitation of the base materials plays a considerable function. Contaminants such as rust, oil, or dampness can evaporate throughout welding, developing gas pockets within the weld. Welding specifications, including voltage, present, travel rate, and electrode type, also impact porosity formation. Making use of inappropriate settings can produce extreme spatter or heat input, which consequently can cause porosity. Moreover, the welding method utilized, such as gas steel arc welding (GMAW) or protected steel arc welding (SMAW), can influence porosity formation as a result of variants browse around these guys in warm distribution and gas insurance coverage. Understanding and controlling these elements are crucial for lessening porosity in welding procedures.
Results of Porosity on Weld Top Quality
Porosity development dramatically jeopardizes the structural stability and mechanical residential or commercial properties of bonded joints. When porosity exists in a weld, it develops gaps or dental caries within the material, decreasing the total toughness of the joint. These spaces act as stress concentration factors, making the weld extra prone to breaking and failure under lots. The existence of porosity likewise damages the weld's resistance to corrosion, as the trapped air or gases within deep spaces can respond with the surrounding setting, bring about destruction with time. In addition, porosity can impede the weld's capability to stand up to pressure or impact, further threatening the total top quality and integrity of the welded structure. In vital applications such as aerospace, automobile, or architectural buildings, where security and longevity are paramount, the detrimental results of porosity on weld top quality can have serious repercussions, highlighting the significance of reducing porosity through proper welding techniques and treatments.
Methods to Minimize Porosity
To boost the top quality of bonded joints and make certain structural integrity, welders and makers utilize certain methods focused on minimizing the formation of voids and tooth cavities within the material during the welding why not try these out procedure. One effective method to minimize porosity is to ensure appropriate material prep work. This consists of detailed cleansing of the base steel to eliminate any contaminants such as oil, oil, or wetness that can add to porosity development. Additionally, using the appropriate welding specifications, such as the appropriate voltage, present, and take a trip speed, is vital in avoiding porosity. Preserving a constant arc size and angle throughout welding also assists reduce the chance of porosity.

Moreover, choosing the appropriate protecting gas and maintaining correct gas flow prices are necessary in lessening porosity. Utilizing the ideal welding strategy, such as back-stepping or employing a weaving movement, can likewise help distribute warm equally and minimize the chances of porosity development. Ensuring correct air flow in the welding setting to eliminate any possible sources of contamination is essential for attaining porosity-free welds. By implementing these techniques, welders can properly reduce porosity and produce high-quality welded joints.
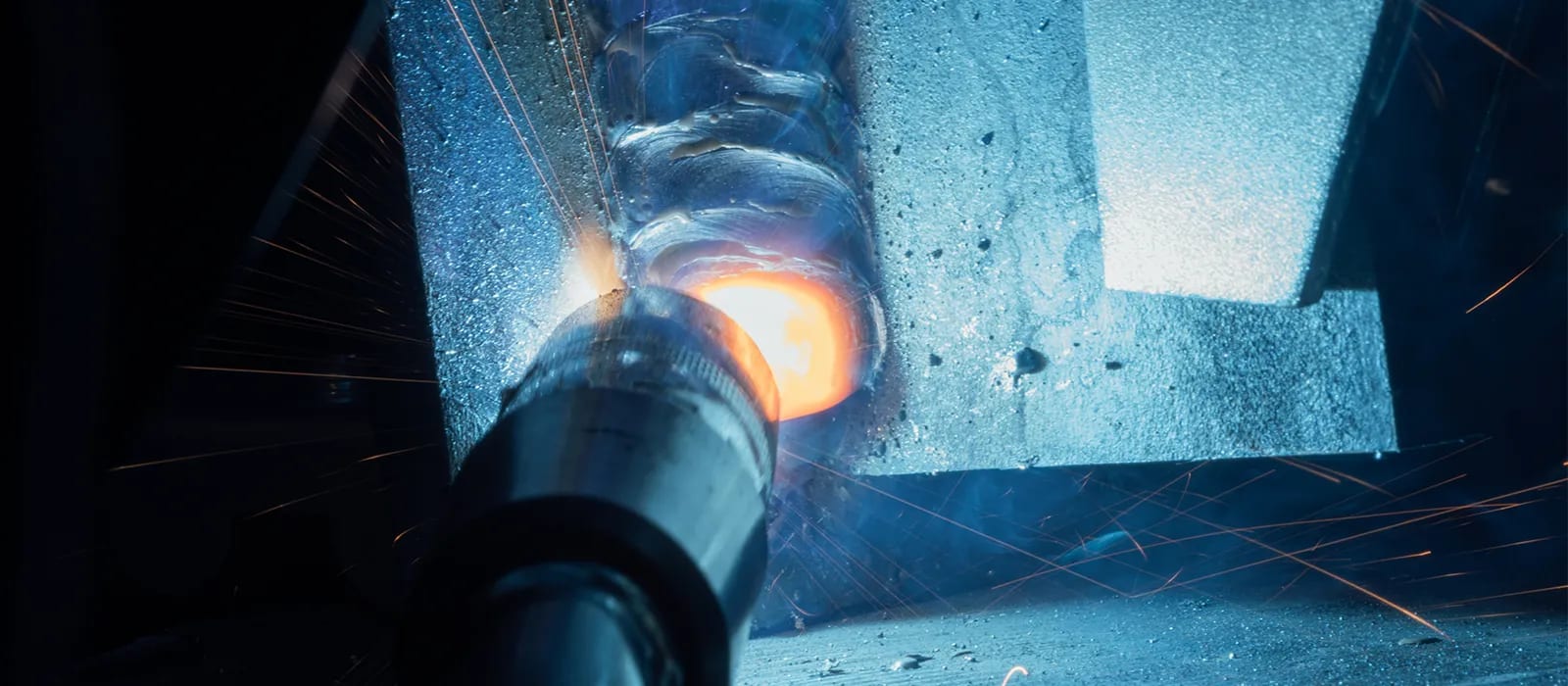
Advanced Solutions for Porosity Control
Carrying out innovative modern technologies and innovative techniques plays a critical role in attaining premium control over porosity in welding processes. Additionally, utilizing innovative welding techniques such as pulsed MIG welding or customized ambience welding can likewise help reduce porosity issues.
One more advanced remedy entails the use of innovative welding devices. For example, using devices with built-in functions like waveform control and advanced source of power can enhance weld high quality and look at this now decrease porosity dangers. The application of automated welding systems with specific control over parameters can substantially lessen porosity issues.
In addition, including innovative surveillance and examination modern technologies such as real-time X-ray imaging or automated ultrasonic screening can assist in identifying porosity early in the welding procedure, permitting for instant restorative actions. In general, integrating these advanced solutions can greatly boost porosity control and boost the general quality of welded components.
Conclusion
In verdict, recognizing the science behind porosity in welding is crucial for welders and makers to create top quality welds - What is Porosity. Advanced remedies for porosity control can even more boost the welding procedure and ensure a strong and reliable weld.